Field of invention: filtration membrane envelope to be used in water treatment, more particularly water filtration and wastewater purification
Applicant: Blue Foot Membranes
Inventors: Peter AERTS, Ulrich BRÜSS, Stephan VAN HOOF
Patent number: WO2023/144409
The problem
The lifetime of currently known integrated permeate channel (IPC) membranes in membrane bioreactors for wastewater treatment is compromised because the multiple layers tend to delaminate. In addition, membranes cast on a woven or knitted textile substrate are susceptible to compression.
Therefore, there is a need to develop a filtration membrane envelope with fine-tuned thickness specifications and improved mechanical properties, which maintain their stiffness, do not delaminate and have good compression resistance during assembly and end-use applications in both filtration and backwash modes.
The objective of the present invention is to provide a filtration membrane envelope with fine-tuned thickness specifications that eliminates these disadvantages.
The solution
Blue Foot's invention provides a filtration membrane envelope comprising a 3D spacer fabric having upper and lower surfaces bonded together and spaced apart by monofilament yarns.
The 3D spacer fabric is sandwiched between two membrane layers forming a permeate channel, the membrane layers being cast respectively on the upper and lower fabric surfaces of the 3D spacer fabric. The upper and lower fabric surfaces are at least partially embedded in the membrane layers forming an upper and lower anchorage section, wherein the anchorage section has a minimum thickness of 100 microns.
The anchoring section has been found to provide good anchorage of the various components of the membrane envelope, to the extent that delamination or peeling under high pressure is prevented. Overall, the envelope is able to maintain its mechanical properties even after extensive use.
The invention relates to a filtration membrane envelope for wastewater purification. The invention also relates to a filtration module comprising an array of planar membrane shells and a method of using the filtration membrane shell or filtration module.
The anchoring portion is defined as the portion of the 3D spacer fabric embedded in either the upper or lower membrane layer. It has been observed that a membrane envelope with an anchorage section should have a minimum thickness in order to make the membrane envelopes sufficiently robust to withstand the high pressures exerted during operational activity and backwashing. No peeling or delamination is observed in this case. In addition, the inventors have observed that the membrane envelopes of the invention do not swell or expand in length or thickness when operated under submerged conditions.
The thickness of the anchorage section and the thickness of the membrane and filtration layers ensure the excellent properties of the membrane envelopes. They are strong, highly compressive and flattening resistant, and do not expand in length or width when operated under submerged conditions. They also exhibit less than 10% peeling or delamination of the spacer fabric and membrane layers when subjected to a pressure of 2 bar, preferably less than 5% peeling or delamination, preferably less than 1% peeling or delamination, or even 0%. The percentage of peeling or delamination is understood to be the amount of membrane layer surface that separates from the 3D spacer fabric.
The permeate channel comprises open spaces formed by said 3D spacer fabric. In order to ensure optimum flow distribution through the membrane envelopes, the percentage of open spaces in the permeate channel is between 80 and 99%, more preferably between 85 and 99%, more preferably between 90 and 99%.
Preferably, the 3D spacer fabric is of a knitted, woven or non-woven type. In a preferred embodiment, the 3D spacer fabric has a woven structure. In one embodiment, the 3D spacer fabric preferably comprises a material selected from the group consisting of polyester, nylon, polyamide, polyphenylene sulfide, polyethylene and polypropylene. During the weaving process, the longitudinal or longitudinal warp yarns are held stationary under tension on a frame or loom while the transverse weft is drawn through and inserted over and under the warp.
The membrane envelope may be made by providing a 3D spacer fabric comprising an upper and lower surface fabric spaced apart by a predetermined distance by monofilament yarns and subsequently applying a membrane layer to the upper and lower surface fabrics such that a plurality of regions are embedded in the membrane layers. The step of applying the membrane layers preferably comprises a casting step with casting materials and coagulation of the cast material to form a membrane layer in which the fabric is embedded. This process is known as "immersion precipitation", where a polymer plus solvent (polymer solution) is cast onto a support layer and then immersed in a coagulation bath containing non-solvent. The exchange of solvent and non-solvent causes precipitation.
The membrane envelope or water filtration module described herein can be used for microfiltration, ultrafiltration, MBR, pervaporation, membrane distillation, supported liquid membranes and/or percolation.
Advantages
- The membrane envelope of the invention does not expand in length or width when submerged. The structure of the membrane envelope, with the 3D spacer fabric and monofilament yarns embedded in the membrane layers, ensures that the membrane envelope maintains its shape and dimensions when submerged in a liquid without expanding. This allows the membrane shell to remain in place during water filtration operations without the use of additional membrane stabilisation means, such as comb-like structures, etc.
- The anchoring section allows good anchoring of the various components of the membrane envelope, to the extent that delamination or peeling is prevented when subjected to high pressures.
- The prior art membranes do not have the excellent mechanical properties of the membrane of the invention, and the thicknesses of the layers and the ratios between these layers are unknown for these prior art membranes.
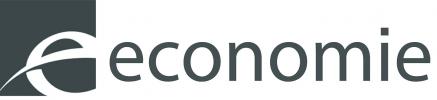